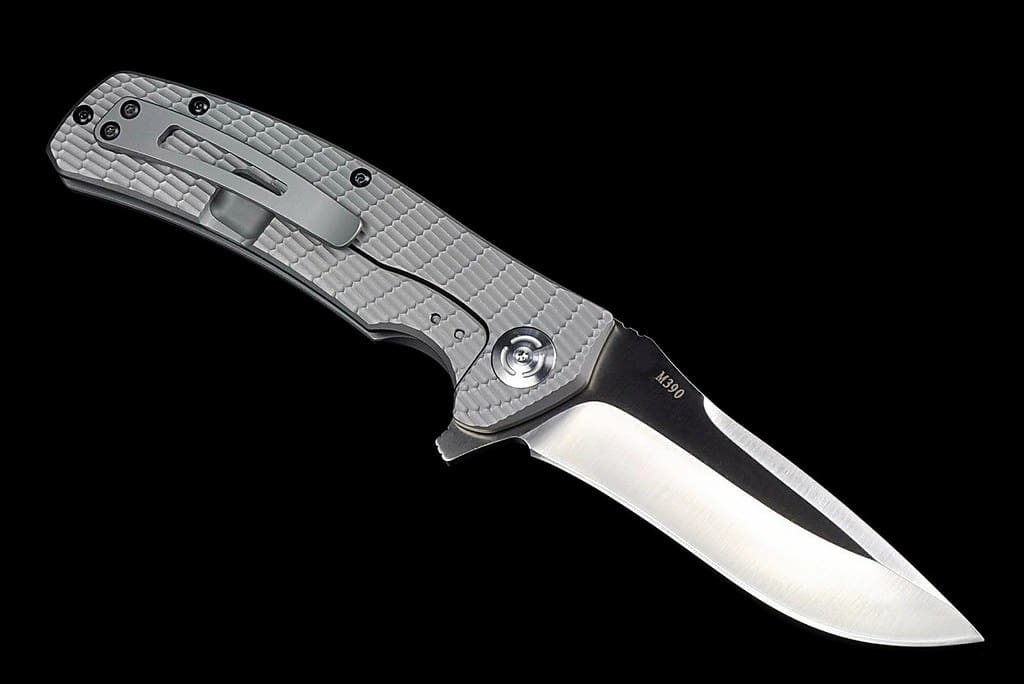
Table of Contents
Introduction
Steel, a seemingly age-old companion to humanity, has evolved tremendously over the years. From the rustic iron used in medieval weaponry to the refined alloys in modern tools, it has always been at the forefront of innovation. Enter M390 steel, one of the high-performance marvels of the metallurgical world. This specialized alloy has become the go-to choice for a variety of industrial applications. And like any prized possession, it demands meticulous handling.
Drilling, an elemental process in metalwork, becomes a true art form when applied to such premium materials. This art form is not only about the technique but also about the choice of tools. For M390 steel, the stakes are even higher. The reason? This isn’t your ordinary steel. Drilling through it requires bits that are not just tough, but bits that embody precision, durability, and performance at their core. This is where the right bits for drilling M390 steel come into play.
In this guide, you’ll embark on a journey to unravel the complexities of M390 steel and understand the sheer importance of equipping yourself with the right drilling bits. Let’s plunge into this intriguing world of steel and the masterful art of drilling it!
The Challenges of Drilling M390 Steel
Imagine a knight attempting to penetrate a dragon’s scales with an ordinary dagger, or a sailor attempting to navigate treacherous seas with a mere paper map. The challenges in both scenarios are monumental and demand tools and skills that are a cut above the rest. Drilling M390 steel presents a similar challenge for metallurgists and craftsmen. So, why is this seemingly unyielding steel so notoriously challenging to work with?
Understanding M390’s Tenacity
It’s essential to first grasp what makes M390 a coveted steel in the industry. Boasting an impressive mix of chromium, molybdenum, vanadium, and tungsten, M390 is not just any regular steel; it’s a super steel. This alloy is celebrated for its corrosion resistance, supreme wear resistance, and impressive hardness.
But with great power, as they say, comes great responsibility. This unmatched hardness, while a boon for durability, turns into a bane for those trying to drill through it. M390’s high wear resistance means it will wear out lesser bits in no time, often leading to inaccuracies in drilling or even ruining the workpiece.
The Thermal Challenges
When you drill through materials, especially something as tenacious as M390 steel, heat is generated. Now, while many steels can handle a degree of heat without any significant impact on the drilling process, M390 is particularly sensitive to it. The heat can rapidly diminish the bit’s life, and without appropriate cooling mechanisms in place, you might find yourself replacing bits far more often than anticipated.
Material Consistency and Bit Bite
The homogeneous nature of M390 steel can pose another unique challenge. Without inconsistencies or “soft spots”, the bit needs to exert consistent force throughout the drilling process. This requirement can be taxing on both the bit and the operator, demanding unwavering precision and pressure. A bit that isn’t sharp enough, or one that’s not designed for such consistency, can slip or fail to penetrate the material, leading to subpar results or, worse, accidents.
In essence, while M390 steel’s attributes make it a darling of the tooling world, these very attributes also demand utmost respect and care when it comes to drilling. Next, we’ll delve into how you can overcome these challenges by selecting the right bits for drilling M390 steel.
Selecting the Right Bits for Drilling M390 Steel
Now that we’ve unraveled the complexities of M390 steel, it’s time to arm ourselves with the right tools to tame this metal giant. Much like a jeweler choosing the perfect gem for a masterpiece, selecting the ideal bits for drilling M390 steel is both an art and a science. Let’s begin our exploration of this intricate process.
Factors to Consider
Selecting the perfect bit isn’t as straightforward as grabbing the sharpest one off the shelf. Several critical considerations come into play:
- Material Composition: Bits made of high-speed steel (HSS) or cobalt are typically recommended for hard metals. Cobalt, in particular, can handle the heat generated while drilling better than most other materials.
- Bit Tip: A split point tip can be highly effective for M390 due to its precision and ability to start drilling without a pilot hole.
- Coating: Coatings like Titanium Nitride (TiN) or Titanium Carbon Nitride (TiCN) can enhance the bit’s performance, longevity, and heat resistance.
- Flute Design: A parabolic flute design facilitates better chip evacuation, ensuring smoother drilling, especially in deep holes.
While these considerations offer a blueprint for decision-making, it’s equally vital to understand that each drilling scenario might demand specific nuances. For instance, drilling deep holes may require bits with enhanced cooling channels, while surface drilling might prioritize precision over heat dissipation.
Recommendations
Based on the aforementioned criteria and the collective wisdom of the metallurgy and hardware community, here are some top bits that have gained acclaim for drilling M390 steel:
- Drill America Cobalt Drill Bit: Known for its robustness and durability, this cobalt bit boasts a gold oxide finish that offers commendable heat resistance.
- Bosch CO21 Cobalt Twist Drill Bit: Celebrated for its split-point tip and long lifespan, this bit is adept at precise drilling without any wandering.
- DEWALT Pilot Point Industrial Cobalt Drill Bit: With its unique Pilot Point tip and heavy-duty cobalt design, this bit assures both accuracy and longevity when tackling M390 steel.
Remember, while these recommendations serve as a guiding light, your specific requirements, machine setup, and drilling conditions play pivotal roles. It’s always wise to consult with product manufacturers or experienced metallurgists to fine-tune your choices.
Armed with the right bits, the journey doesn’t end here. Let’s dive deeper and understand the techniques to make the drilling process as efficient and effective as possible.
Tips for Effective Drilling
Having the right bit is just half the battle won. To truly master the art of drilling through M390 steel, one must adopt the right techniques and methodologies. Let’s journey together through some of these magical tips and tricks that can make the drilling process smoother, more effective, and, dare we say, almost enchanting!
- Start Slow: Launching into a high-speed drilling frenzy might sound thrilling, but it’s a quick recipe for disaster. Begin at a slower speed, ensuring you get a feel for the material before increasing the RPMs.
- Lubrication is Key: Keep the drill bit well-lubricated. This not only reduces the heat produced but also minimizes the risk of the bit getting stuck or wearing out prematurely.
- Constant Pressure: Maintaining a steady pressure ensures consistent drilling. Too much force can break the bit, while too little can lead to uneven holes.
- Regular Breaks: Periodic pauses are not just for the driller but also for the drill bit. It helps in cooling down, reducing wear, and ensuring longer life for the tool.
- Use Pilot Holes: For larger holes, start with a smaller pilot hole. It guides the larger bit and reduces the risk of wandering or breaking.
- Clear Chips Frequently: Regularly clear away the metal chips. This not only ensures clear visibility but also aids in better heat dissipation.
Now, imagine yourself in the midst of a grand symphony, where you’re the maestro and the drill bit is your baton. The M390 steel lies in front of you like a canvas, waiting for your magic touch. As you follow these guidelines, you’ll notice the metal yielding, almost dancing to your tunes. It’s a harmony of man, machine, and metal!
While the euphoria of successful drilling can be intoxicating, it’s essential not to lose sight of the importance of safety. In our next section, we’ll explore how to ensure that your drilling adventures remain not just effective but safe as well.
Safety Considerations
As the ancient adage goes, “Safety first!” And when it comes to drilling, especially into something as tough and unforgiving as M390 steel, this phrase holds even truer. Taking a moment to ensure your safety can mean the difference between a successful project and an unfortunate mishap. Let’s embark on this vital journey through safety’s sacred sanctuary.
Protective Gear
The armor you don becomes the guardian angel of your drilling endeavors. Always make sure you’re equipped with the following:
- Goggles: Protect your eyes from flying shards of metal and other debris.
- Gloves: Insulate your hands from the vibrations of the drill and protect them from potential cuts.
- Ear Protection: Drilling can be loud, especially on metal. Preserve your hearing by using earplugs or earmuffs.
Workspace Safety
The sanctity of your workspace is paramount. Here’s how to keep it safe:
- Well-lit Area: Proper lighting ensures you see exactly where you’re drilling, preventing mishaps.
- Clean Workspace: Free of clutter, a clean workspace minimizes tripping hazards and other accidents.
- Secure the Material: Use clamps or vises to hold the M390 steel in place. A moving workpiece can be dangerous!
Drill Maintenance
Like a knight polishing his sword, taking care of your drill ensures it doesn’t turn on you:
- Regular Inspection: Check your drill and bits for wear or damage before each use.
- Sharp Bits: Dull bits require more pressure and can slip, increasing the risk of accidents. Keep them sharp!
- Unplug When Not in Use: An unattended, plugged-in drill is a safety risk. Always unplug it when you’re not using it.
In the grand dance of drilling, safety sets the rhythm. It orchestrates the movements, guiding you gracefully between steps. By ensuring you’re safe, you are free to explore the world of drilling with confidence and joy. And speaking of joy, our journey through the realm of drilling M390 steel is coming to its crescendo. Let’s dive into the conclusion to wrap up our adventure!
Conclusion
As we conclude our deep dive into the vast sea of drilling M390 steel, it’s evident that the dance between machine and metal is intricate, demanding, but exceptionally rewarding. Crafting with such a robust material like M390 steel is not just about having the right equipment or skills—it’s a marriage of knowledge, patience, and due diligence.
From understanding the unique challenges posed by M390 steel, navigating through the maze of drill bit selection, to imbibing tried and tested drilling strategies, we’ve sailed through them all. And let’s not forget the golden rules of safety that guard our ventures.
Reflect and Progress
But as with all things in the realm of creation, knowledge is an evolving entity. The recommendations and techniques mentioned today will undoubtedly be refined with time and technological advancements. It’s essential for enthusiasts and professionals alike to stay updated, share experiences, and contribute to the ever-expanding community knowledge.
Embark and Create
The world of M390 steel drilling is filled with opportunities. Whether you’re crafting a beautiful piece of jewelry, designing a robust tool, or embarking on a DIY project, remember that every spin of the drill bit is a step towards mastery. So, gear up, set your focus, and let the symphony of metal and machine play!
Thank you for joining us on this enlightening journey. As you move forward, armed with knowledge and insight, may your drilling ventures be smooth, safe, and successful. Until next time, keep creating, innovating, and always drilling forward!