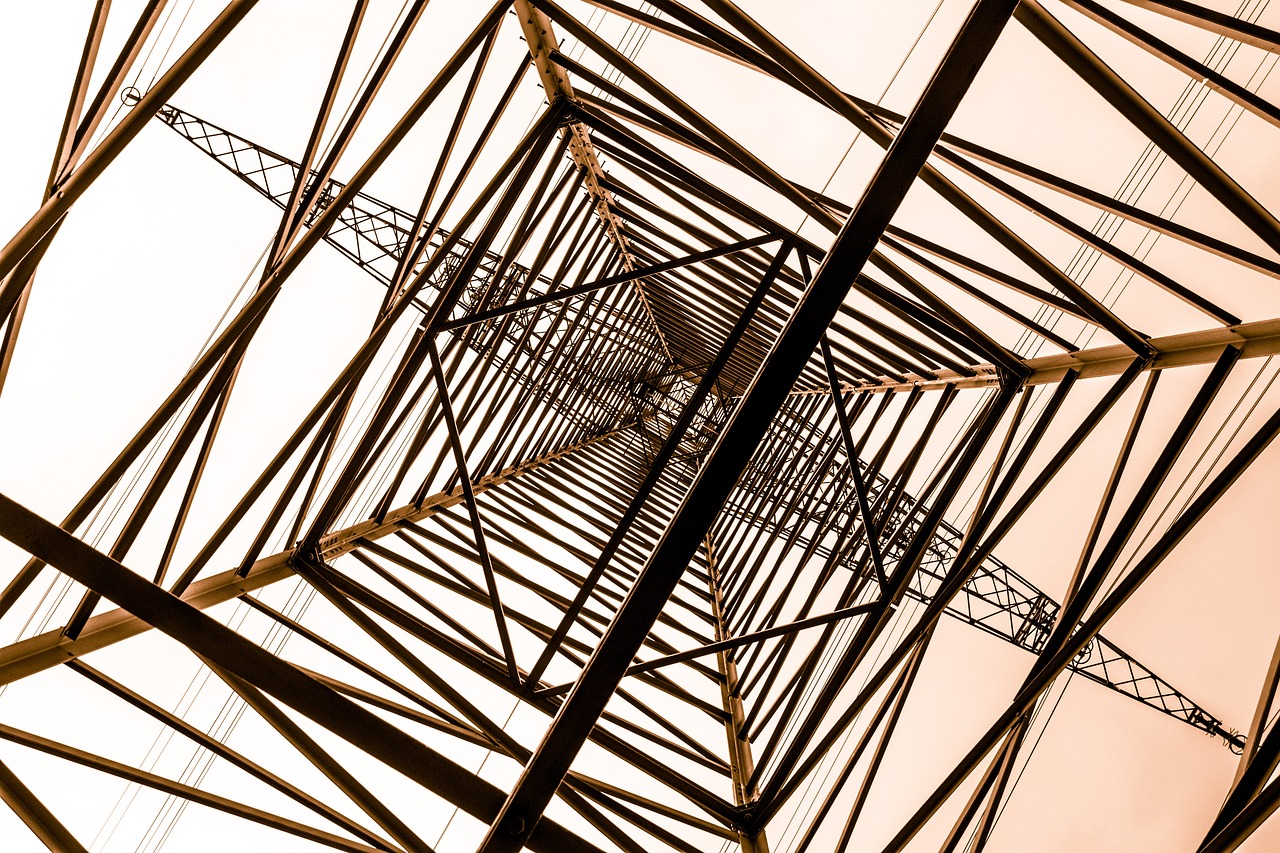
Table of Contents
Introduction
440 steel, renowned for its strength and resilience, is often the choice of material for tools, ball bearings, and even knives. However, as is often the case with sturdy materials, the process of drilling into them requires both precision and the right tools. This is not just about ensuring a clean drill but also about ensuring longevity for both the steel and the drill bit. This article serves as an in-depth guide to bits for drilling 440 steel.
Understanding 440 Steel
The allure of 440 steel is its blend of characteristics. It’s not just about toughness; this steel type also boasts impressive resistance to wear, rust, and corrosion. But what makes 440 steel tick? Let’s delve deeper.
Characteristics of 440 Steel
440 steel belongs to the stainless steel family, specifically the 440 series which includes 440A, 440B, and 440C. Here’s what sets it apart:
- Hardness: Among the stainless steels, 440 is notably hard, making it a popular choice for knife blades.
- Wear Resistance: Its hardness directly contributes to its wear resistance, ensuring it doesn’t wear out easily with friction or use.
- Corrosion Resistance: 440 steel’s chromium content aids its resistance to rust, making it apt for moist environments.
Challenges Faced When Drilling into 440 Steel
With its suite of admirable characteristics, 440 steel is not the easiest to work with. Drilling into it presents a set of challenges:
- Heat Generation: Drilling generates friction, and when it comes to 440 steel, this friction can lead to significant heat. This not only affects the drill bit’s lifespan but can also temper the steel itself.
- Bit Wear: The hardness of 440 steel can lead to rapid wear of drill bits, especially if they aren’t of high quality or apt for the job.
- Accuracy: The tough nature of 440 steel might result in drill bits wandering or deflecting, especially if not used at the right speed or without appropriate pressure.
Given these challenges, it’s evident that choosing the right drill bit isn’t just a matter of convenience but also of efficiency and economy. Let’s understand how to make this crucial choice.
Understanding 440 Steel
Steels come in a spectrum of grades, and among them, the 440 steel has carved a niche for itself due to its distinctive properties. Renowned for its hard-wearing nature and resistance to external elements, it’s no wonder that 440 steel has found its way into critical applications such as surgical instruments, cutting tools, and bearings. But to truly appreciate its essence, it’s imperative to deep dive into its intrinsic characteristics and the challenges it poses when drilling.
Characteristics of 440 Steel
Understanding any metal begins with recognizing its core features, and 440 steel is no different:
- Hardness: A standout trait, 440 steel’s hardness level makes it a prime choice for tools that demand durability. Especially when it comes to the 440C variant, we’re talking about one of the hardest stainless steels available.
- Wear Resistance: This steel’s toughness ensures it doesn’t wear down easily even under constant friction or rigorous use, making it an asset in high-abrasion environments.
- Corrosion Resistance: Owed largely to its substantial chromium content, 440 steel resists rust and corrosion, marking its suitability for wet or humid settings.
Challenges Faced When Drilling into 440 Steel
Superior characteristics aside, 440 steel isn’t the friendliest when it comes to drilling. Working with this steel grade comes with its own set of challenges:
- Heat Generation: Friction is a given when drilling, but with 440 steel, this friction escalates to produce remarkable heat. This isn’t merely a threat to the drill bit’s longevity; it can also compromise the steel’s temper, impacting its properties.
- Bit Wear: The pronounced hardness of 440 steel can be taxing on drill bits, causing them to wear out at an accelerated rate, particularly if they aren’t ideally suited for the task.
- Accuracy Concerns: 440 steel’s tough nature might lead drill bits astray, causing them to drift or deflect if not operated at the optimal speed or pressure, thereby affecting the precision of the drilling.
Confronted with these challenges, the question arises: How does one effectively drill into 440 steel? The answer lies in the drill bit’s selection, a topic we will unravel in the subsequent sections.
Factors to Consider Before Choosing Bits for Drilling 440 Steel
As established, drilling into 440 steel is no walk in the park. But with the right drill bit, half the battle is won. Before delving into specific types of drill bits, let’s explore the various factors that should inform your choice.
Material of the Drill Bit
The material of the drill bit plays a pivotal role in determining its performance, especially when tackling hard substances like 440 steel. Here’s a breakdown:
- High-Speed Steel (HSS): Known for its ability to withstand high temperatures, HSS bits are durable and apt for drilling into metals. However, when it comes to harder alloys like 440 steel, they might wear out quicker unless coated.
- Carbide-Tipped: These bits have carbide tips fused to their cutting edge. They are incredibly hard and can endure the toughness of 440 steel, but they can be brittle and might break with undue pressure.
- Cobalt: Made of solid cobalt alloys, these bits are a notch above HSS when it comes to hardness and heat resistance. They’re particularly suited for drilling into hard metals.
Bit Geometry and Point Angle
The shape and design of a drill bit significantly affect its drilling prowess:
- 118° Point: This is the standard angle for many drill bits. They are great for drilling into soft materials but might not be the best choice for hard steels.
- 135° Self-Centering Point: These have a flatter point and are perfect for hard materials like 440 steel. The self-centering nature ensures accuracy and reduces the wandering of the bit.
Coating and Finish
A drill bit’s coating isn’t just about aesthetics. It can enhance its performance and lifespan substantially. Here’s a glance at popular coatings:
- Titanium Nitride (TiN): This golden coating adds hardness to the drill bit and reduces friction, thus increasing its lifespan. Particularly useful when drilling into hard steels.
- Black Oxide: Enhances heat resistance and prolongs tool life. Also, it offers a degree of corrosion resistance.
- Diamond Powder Coating: Ideal for high-abrasion tasks, these bits offer superior wear resistance and longevity.
With these factors in perspective, let’s delve into the specific types of drill bits best suited for 440 steel. Their understanding will guide you towards making an informed choice, ensuring efficiency, safety, and value for money.
Types of Drill Bits Suitable for 440 Steel
Having delved into the intricacies of 440 steel and the factors influencing the selection of drill bits, let’s address the heart of the matter: the types of drill bits that rise to the challenge of 440 steel. Remember, it’s not just about drilling, but drilling right. The goal is to achieve precision without sacrificing bit longevity. Here’s the lowdown:
High-Speed Steel (HSS) Drill Bits with Titanium Coating
When HSS bits are infused with a Titanium Nitride (TiN) coating, they transform into formidable tools for drilling metals, including tough ones like 440 steel. The TiN coating doesn’t just offer a shiny gold aesthetic; it amplifies the bit’s hardness, reduces heat generation through friction, and prolongs lifespan by reducing wear. But there’s a catch: always ensure you’re using a fresh, sharp TiN-coated HSS bit for the best results.
Cobalt Drill Bits
Constructed from solid cobalt alloys, cobalt bits are a force to be reckoned with. These bits are engineered for drilling into hard metals, making them perfect for 440 steel. Their intrinsic hardness, combined with superior heat resistance, ensures that they don’t give in to the challenges posed by such steels. If precision and longevity are your primary concerns, cobalt bits are the way to go.
Carbide-Tipped Drill Bits
Stepping into the premium territory, carbide-tipped bits are the pinnacle of drilling technology when hard metals are in question. The extreme hardness of carbide ensures that these bits remain unfazed even when faced with the Herculean task of drilling 440 steel. However, their strength is also their weakness. Carbide is brittle, meaning excessive pressure or a sudden jerk can lead to breakage. Hence, while these bits promise unmatched performance, they demand a skilled hand and attentive care during operation.
Split Point Drill Bits
A twist on traditional designs, split point bits have a modified angle, usually around 135°. The result? A self-centering bit that eliminates the need for a center punch. As they initiate drilling, their design ensures reduced bit walking and enhanced precision, which is invaluable when working with tough materials where accuracy is paramount.
Diamond Core Drill Bits
These are the luxury cars of the drilling world. As the name suggests, diamond core bits have diamond-infused edges. Given diamond’s status as the hardest natural material, these bits can effortlessly pierce through 440 steel. Besides their impressive performance, they also promise longevity, ensuring that the initial investment pays off in the long run.
In conclusion, while 440 steel can be daunting, with the right drill bit, the task becomes exponentially more manageable. The key is understanding the steel’s challenges and then picking a bit that not only addresses but overcomes them.
Caring and Maintenance Tips for Drill Bits
Equipped with the right drill bit, one can confidently embark on the journey of drilling through 440 steel. However, having the right tool is only part of the equation. Maintaining its pristine condition ensures that its performance remains consistent, and its lifespan gets extended. In this section, we’ll explore some practical ways to take care of your drill bits, ensuring they’re always up for the challenge.
Regular Cleaning
After a rigorous drilling session, it’s not uncommon for bits to be cloaked in debris, oil, or metal shavings. Allowing these to linger not only affects the bit’s efficiency but can also lead to premature wear. Here’s how to clean them:
- Soak the bit in a cleaning solution, ideally one made for metals. A few minutes should suffice.
- Using a brush with soft bristles, gently scrub away the accumulated grime.
- Rinse with clean water and dry thoroughly before storing.
Regular Sharpening
A dull bit is a bit’s worst enemy. Not only does it reduce efficiency, but it also augments the wear rate, shortening its lifespan. To counter this:
- Invest in a drill bit sharpener. These devices are purpose-built and ensure a uniform sharpening angle.
- For those averse to machines, a diamond file can also do the trick. However, this requires a steady hand and an understanding of the correct sharpening angle.
- Always test the bit on a scrap piece of material after sharpening to ensure its efficacy.
Proper Storage
The manner in which you store your bits can significantly influence their longevity:
- Always keep them in a cool, dry place to ward off rust and corrosion.
- Use storage solutions like drill indexes or pouches that offer individual slots for each bit, minimizing the risk of them rubbing against each other.
Avoid Overheating
Heat is a perennial challenge when drilling, more so with hard materials like 440 steel. Excessive heat can not only damage the bit but also the material being drilled:
- Always use cutting fluids or coolants, especially when drilling metals.
- If the bit becomes too hot to touch, pause the drilling and allow it to cool naturally. Forced cooling, like dipping a hot bit in cold water, can cause it to warp or crack.
Operate with Care
While it might be tempting to apply brute force, especially when faced with resilient materials, restraint is key:
- Always start with a low speed and gradually increase as the bit finds its rhythm.
- Too much pressure can cause the bit to break, especially brittle ones like carbide-tipped bits.
In essence, while choosing the right bit for drilling 440 steel is paramount, maintaining it with care ensures that it remains a trusty companion for all your drilling endeavors.
Conclusion
Drilling through 440 steel, a material known for its toughness, calls for both skill and the right tools. Equipped with the proper knowledge about the steel and the bits that are tailored to cut through it, the task becomes exponentially easier. But, as we’ve learned throughout this article, merely possessing the right drill bit isn’t the end of the story.
Understanding the nuances of 440 steel sets the stage for an efficient drilling operation. Its hardy nature, resistance to wear, and impressive strength make it an appealing choice for various applications, but also a challenging adversary for any drill bit. By recognizing the key factors to consider, from bit material to drill speed, we ensure that we’re well-prepared to tackle this challenge head-on. The realm of drill bits offers us a variety of choices. Cobalt, carbide-tipped, and black oxide bits each bring unique strengths, with the underlying promise of making our drilling operation smoother and more efficient.
However, the longevity and efficiency of these bits hinge heavily on the care they receive. Regular maintenance, correct usage, and proper storage all play a vital role in ensuring that our bits remain in optimal condition, ready to take on 440 steel at a moment’s notice.
In conclusion, the journey of drilling through 440 steel is one of preparation, understanding, and care. With the right bit in hand, complemented by a regimen of regular maintenance, there’s no piece of 440 steel too tough to penetrate. As with any task, knowledge is power, and equipped with the insights from this article, you’re well-prepared to tackle any drilling challenge that comes your way.